After reading the Larue Billet Lower thread I thought I would clear up some confusion
First off, you must be carefull making blanket statements that "forged is stronger than billet" bla bla bla. As the saying goes , a little bit of knowledge is dangerous, and this is the general result of reading this statement on the internet and passing it off as gospel
Forging vs Billet in GENERAL :
This debate stared years ago with crankshafts / pistons etc . First off cast cranks are nowhere in the performance range because of the material used in CAST IRON / STEEL is drastically different. Therefore cast cranks are weaker due to the metallurgy of a cast steel / iron. This is due to the fact that the steel / iron is optimized so it flows through the mold
Forged is generally stronger because because the grain structure is more continous along the throws ( the zig zag of the crank the connecting rods attatche to for you non gear heads )
Billet is not necessarily bad if done right but the grain structure is less continous across the throws. The reason that billet is used is to make a non standard profile ( throw distance etc ) because it is very expensive to make now forging dies
Having said that, THIS IS ALL IN THEORY because a crappy forging is less desirable than a perfect billet. I have broken a forged crank, but never a billet . Does this mean a forged is not as good...of course not ! A good billet crank is not a BAD thing
Billet vs Forging in Aluminum
Forget what you know about forged / billet ferrous materials because it does not necessarily apply to aluminum
First off, as someone already mentioned a billet can be made from a forged ingot. Generally the term billet LOOSLEY refers to a part that has been machined on all surfaces. So if you you can have a billet forging
Billet however is often made from a solid chunk of wrought aluminum ( rectangular block in the case of an ar upper) . Least desirable is a billet made from a rough aluminum casting (again the alloys are optimized for flowing into the mold )
Strength of Aluminum
The reason that the argument of forged vs billet for aluminum is just academic ( give guys on the internet somthing to do ) is this : UNLIKE most other materials ( ferrous and non ferrous ) aluminums strength is from heat treatment
For reference a 7075 that a typical mi spec forging is made from, AND a billet upper such as the Larue Stealth has the following tensile strength
7075 in "O" Temper TS = 33 ksi
7075 in "T-6" Temper TS = 88 ksi
As you can see the in non heat treated condition its not as strong as typical A36 structural steel. After heat treatment it is FAR stronger
Billet vs Forged Aluminum
Soooooo, back to the old argument, aluminum does not exhibit the benefits for grain alignment as much as ferrous materials as it undergoes the forging process. A forged aluminum might have a slightly better grain structure ( strain hardening - H1 temper ) than a wrought block but this is FAR OUTWEIGHED by the increase in strength that the T-6 heat treatment process provides
BTW - T-6 requries a solution heat treat ( think of it as you put too much sugar in your coffee that it percipitates out to the bottom at room temperature, but is in solution when hot. After that, it goes through artifical aging. A work hardening ( ie, pounding it with a die / hammer ) temper for non heat treatable alloys such as "H-1" does not impart nearly the strength improvement
Conclusion, a forged alumium is not necessarily appreciably stronger than a good billet
Conclusion 2 - unless you are using your AR as a club to beat someone with, even if one was stronger than the other its all achedemic
Why billet AR parts
The forging dies are very expensive ( which is why many AR mfg buy from the same forging houses ) so to make a non standard dimensioned part its much easier
So you can beef up a part by easily using a wrought billet
You can beat the billet vs forged horse to death but you can't argue that from the pictures below most billet uppers are far heavier in certain areas
Top is a Sun Devil Billet, middle a RRA std, bottom is a Vltor MUR ( FORGING ..new MURs are made from a forging )
As you can see the walll thickness is much heavier ( you can see the notch to clear the bolt release ). The Larue Stealth is also much heavier. I will post pics later
So, why do I have billet ( Sun Devil, Larue ) and forged billet style ( Vltor ) uppers. Because for the extra $50 - $100 why not. I won't hesitatate to spend insane amounts of money on good glass, why would I care about $50 over the total cost of a build
First off, you must be carefull making blanket statements that "forged is stronger than billet" bla bla bla. As the saying goes , a little bit of knowledge is dangerous, and this is the general result of reading this statement on the internet and passing it off as gospel
Forging vs Billet in GENERAL :
This debate stared years ago with crankshafts / pistons etc . First off cast cranks are nowhere in the performance range because of the material used in CAST IRON / STEEL is drastically different. Therefore cast cranks are weaker due to the metallurgy of a cast steel / iron. This is due to the fact that the steel / iron is optimized so it flows through the mold
Forged is generally stronger because because the grain structure is more continous along the throws ( the zig zag of the crank the connecting rods attatche to for you non gear heads )
Billet is not necessarily bad if done right but the grain structure is less continous across the throws. The reason that billet is used is to make a non standard profile ( throw distance etc ) because it is very expensive to make now forging dies
Having said that, THIS IS ALL IN THEORY because a crappy forging is less desirable than a perfect billet. I have broken a forged crank, but never a billet . Does this mean a forged is not as good...of course not ! A good billet crank is not a BAD thing
Billet vs Forging in Aluminum
Forget what you know about forged / billet ferrous materials because it does not necessarily apply to aluminum
First off, as someone already mentioned a billet can be made from a forged ingot. Generally the term billet LOOSLEY refers to a part that has been machined on all surfaces. So if you you can have a billet forging
Billet however is often made from a solid chunk of wrought aluminum ( rectangular block in the case of an ar upper) . Least desirable is a billet made from a rough aluminum casting (again the alloys are optimized for flowing into the mold )
Strength of Aluminum
The reason that the argument of forged vs billet for aluminum is just academic ( give guys on the internet somthing to do ) is this : UNLIKE most other materials ( ferrous and non ferrous ) aluminums strength is from heat treatment
For reference a 7075 that a typical mi spec forging is made from, AND a billet upper such as the Larue Stealth has the following tensile strength
7075 in "O" Temper TS = 33 ksi
7075 in "T-6" Temper TS = 88 ksi
As you can see the in non heat treated condition its not as strong as typical A36 structural steel. After heat treatment it is FAR stronger
Billet vs Forged Aluminum
Soooooo, back to the old argument, aluminum does not exhibit the benefits for grain alignment as much as ferrous materials as it undergoes the forging process. A forged aluminum might have a slightly better grain structure ( strain hardening - H1 temper ) than a wrought block but this is FAR OUTWEIGHED by the increase in strength that the T-6 heat treatment process provides
BTW - T-6 requries a solution heat treat ( think of it as you put too much sugar in your coffee that it percipitates out to the bottom at room temperature, but is in solution when hot. After that, it goes through artifical aging. A work hardening ( ie, pounding it with a die / hammer ) temper for non heat treatable alloys such as "H-1" does not impart nearly the strength improvement
Conclusion, a forged alumium is not necessarily appreciably stronger than a good billet
Conclusion 2 - unless you are using your AR as a club to beat someone with, even if one was stronger than the other its all achedemic
Why billet AR parts
The forging dies are very expensive ( which is why many AR mfg buy from the same forging houses ) so to make a non standard dimensioned part its much easier
So you can beef up a part by easily using a wrought billet
You can beat the billet vs forged horse to death but you can't argue that from the pictures below most billet uppers are far heavier in certain areas
Top is a Sun Devil Billet, middle a RRA std, bottom is a Vltor MUR ( FORGING ..new MURs are made from a forging )
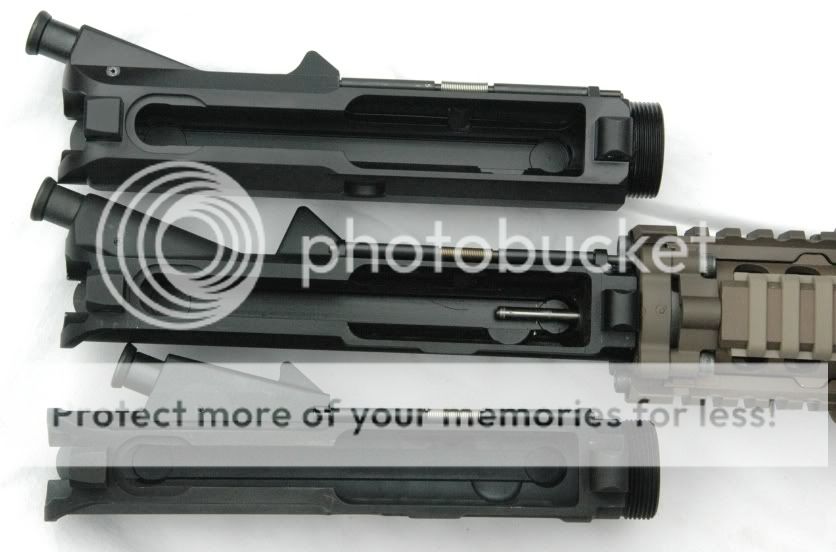
As you can see the walll thickness is much heavier ( you can see the notch to clear the bolt release ). The Larue Stealth is also much heavier. I will post pics later
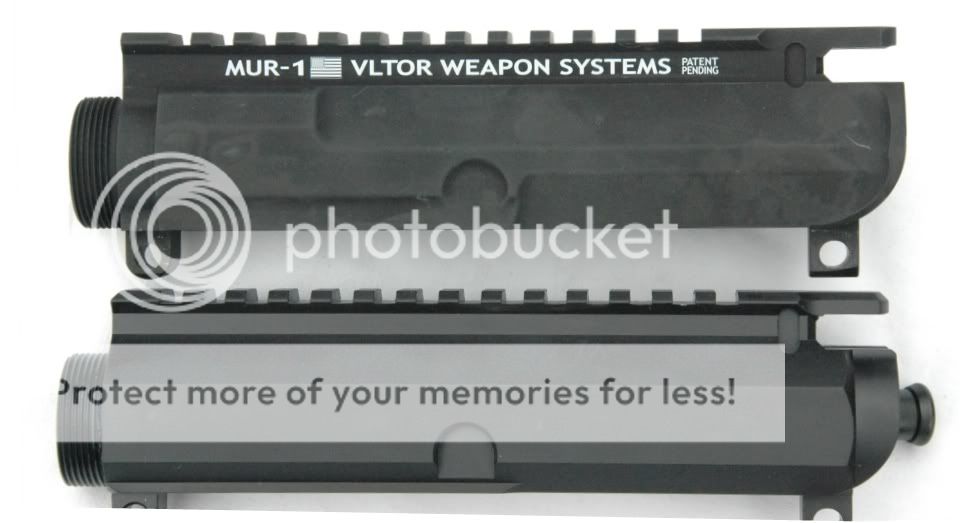
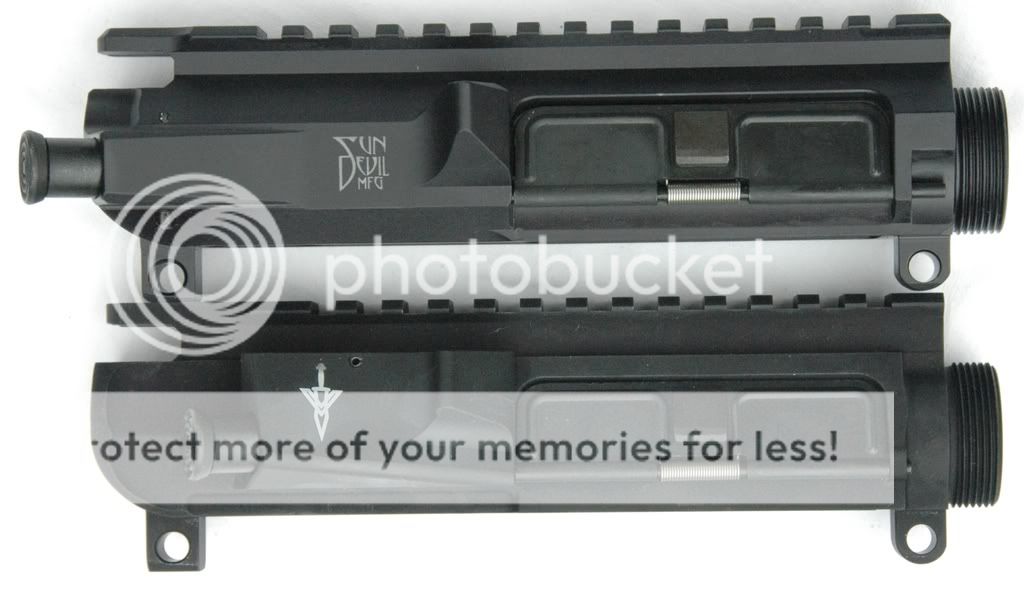
So, why do I have billet ( Sun Devil, Larue ) and forged billet style ( Vltor ) uppers. Because for the extra $50 - $100 why not. I won't hesitatate to spend insane amounts of money on good glass, why would I care about $50 over the total cost of a build
Last edited: