Hey all,
Need some help here, new to reloading and not sure what to do. Started up a resizing and de-priming session last night using a Lee collet neck sizing die on an RCBS Rock Chucker press, and after a couple of successful resize/decaps, the collet appears to have started getting stuck(?) and crushed a couple cases, quickly ending my session. I used the die to do a 100 cases a couple of days prior with no problems, and all of a sudden this. See the attached picture for what it's doing. The collet marks are at the top half of the neck. The case de-primed normally, felt right in the resistance for de-priming and sizing, but the result when I pulled it out was it being crushed. WTF?
Anyone's input would be much appreciated. As mentioned earlier in the post, I'm am a rookie at this. The 100 cases I mentioned resizing were my first.
Thanks in advance.
Need some help here, new to reloading and not sure what to do. Started up a resizing and de-priming session last night using a Lee collet neck sizing die on an RCBS Rock Chucker press, and after a couple of successful resize/decaps, the collet appears to have started getting stuck(?) and crushed a couple cases, quickly ending my session. I used the die to do a 100 cases a couple of days prior with no problems, and all of a sudden this. See the attached picture for what it's doing. The collet marks are at the top half of the neck. The case de-primed normally, felt right in the resistance for de-priming and sizing, but the result when I pulled it out was it being crushed. WTF?
Anyone's input would be much appreciated. As mentioned earlier in the post, I'm am a rookie at this. The 100 cases I mentioned resizing were my first.
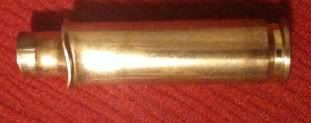
Thanks in advance.
Last edited: