I'm a machinist. I'm also frugal and have free aluminum, tooling and a T1x. I'm throwing around the idea of making my own chassis based off the idea of an LSS from MDT.
https://mdttac.ca/lss-chassis-system/
My biggest questions are where to find the spec sheet for the AR15 grip platform and where you recommend I buy one as well as a buffer tube with adjustable check rests. (or 3D print my own....)
If you check my post history you'll see I've made two stocks from wood with cnc and by hand in the last year. I already have the T1x action entirely modelled in Fusion.
I am also open to the idea of doing a more Gray Birch style stock but I need a 'pad' at the buttstock since I also shoot off bags and put my left hand under the buttstock/on my bicep.
Very odd chance but if there's anyone with a chassis and 3D scanner maybe we can talk...
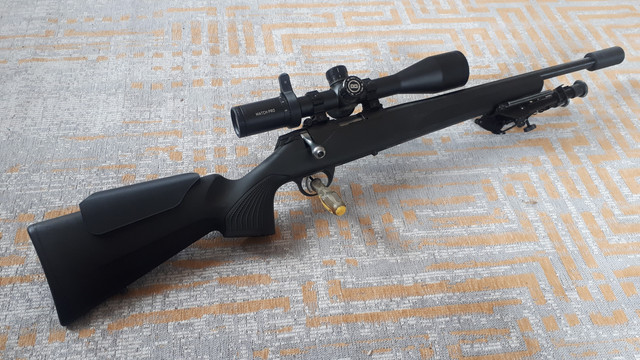
https://mdttac.ca/lss-chassis-system/
My biggest questions are where to find the spec sheet for the AR15 grip platform and where you recommend I buy one as well as a buffer tube with adjustable check rests. (or 3D print my own....)
If you check my post history you'll see I've made two stocks from wood with cnc and by hand in the last year. I already have the T1x action entirely modelled in Fusion.
I am also open to the idea of doing a more Gray Birch style stock but I need a 'pad' at the buttstock since I also shoot off bags and put my left hand under the buttstock/on my bicep.
Very odd chance but if there's anyone with a chassis and 3D scanner maybe we can talk...

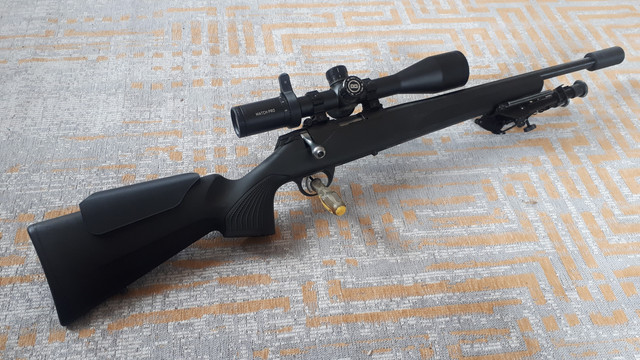
Last edited: