BlackPowderBurner
CGN frequent flyer
- Location
- the chesterfield
I just picked this old school Herters 9 Ton Swaging Press that came with a set of .38/.357 dies installed. It seems like a pretty solid unit! Is anyone else using one of these or has some experience to share? The surface scale was just dried grease that cleaned up nicely with some ballistol, she's all shiny now.
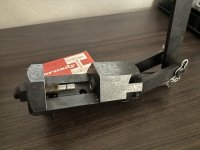
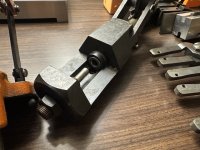
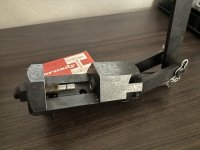
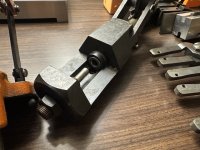