Hi Guys
Recently I fired and fell in love with the 35 Remington, I now have two, both with Ballard rifling for cast lead bullets. A 336 from the 50's and a 760 also from the 50's. I have been having a hard time finding brass in the stores, some CGN veterans helped me out so I have a bunch, thank you to all who helped. But I got to wondering hmmm what am I going to do we run out and they don't make it anymore? So here is what I did...
The 30-06 is a tapered casing that has a shoulder diameter smaller that the head diameter of the 35 rem, hmmm.
So I bought an old 30-06 full sizing die with a broken decaping pin and I cut the top off at the shoulder.
Steps
1 cut the 30-06 shorter to about 2 inches
2 make sure the case its well lubed!
3 used the press and a bottom punch, push the 30-06 case into the cut full sizing die until it measures the correct head diameter for 35 rem.
3.2 Lock the lock ring on the sizing die, so each case after is only pushed to a full stroke.
4 knock the reduced 30-06 case out from the top with a punch.
5 re size the primer flash hole
6 anneal the would be neck, lube, and then resize 30-06 cases.
7 swap the sizing die for 35 remington
8 full size the reduced 30-06 cases to 35 remington.
9 ream out the primer pocket.
10 trim it to length
step 11 will be to recut the extraction groove I hope to do this on a lathe. I still need to set up my lathe into the basement workshop.
Starting with 308 cases allows you to skip the pre cutting of step 1.2, they get cut to final length at the end.
Big thanks to Andy and Mac100!
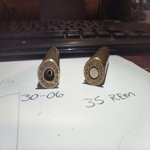
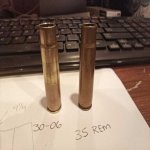
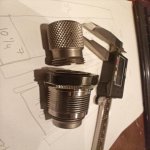
Recently I fired and fell in love with the 35 Remington, I now have two, both with Ballard rifling for cast lead bullets. A 336 from the 50's and a 760 also from the 50's. I have been having a hard time finding brass in the stores, some CGN veterans helped me out so I have a bunch, thank you to all who helped. But I got to wondering hmmm what am I going to do we run out and they don't make it anymore? So here is what I did...
The 30-06 is a tapered casing that has a shoulder diameter smaller that the head diameter of the 35 rem, hmmm.
So I bought an old 30-06 full sizing die with a broken decaping pin and I cut the top off at the shoulder.
Steps
1 cut the 30-06 shorter to about 2 inches
2 make sure the case its well lubed!
3 used the press and a bottom punch, push the 30-06 case into the cut full sizing die until it measures the correct head diameter for 35 rem.
3.2 Lock the lock ring on the sizing die, so each case after is only pushed to a full stroke.
4 knock the reduced 30-06 case out from the top with a punch.
5 re size the primer flash hole
6 anneal the would be neck, lube, and then resize 30-06 cases.
7 swap the sizing die for 35 remington
8 full size the reduced 30-06 cases to 35 remington.
9 ream out the primer pocket.
10 trim it to length
step 11 will be to recut the extraction groove I hope to do this on a lathe. I still need to set up my lathe into the basement workshop.
Starting with 308 cases allows you to skip the pre cutting of step 1.2, they get cut to final length at the end.
Big thanks to Andy and Mac100!
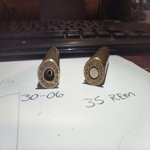
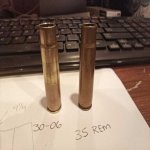
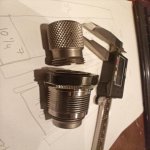
Attachments
Last edited: