Vaterslote
Member
- Location
- Belleville, On
Hello help.
I have a TWIGG pocket pistol that the trigger appears to have had some work done shortening it enough to that it will not engage the #### and half ####. I suspect that this CANNOT we welded no to add metal. Any suggestions. I need about 1/16th added to the top of the trigger to engage onto the bottom of the hammer.
Also looking for someone that can make me a spring for this Muff Pistol. Appreciate any leads you can offer. Willing to ship or drive from Belleville On.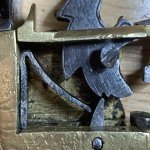
I have a TWIGG pocket pistol that the trigger appears to have had some work done shortening it enough to that it will not engage the #### and half ####. I suspect that this CANNOT we welded no to add metal. Any suggestions. I need about 1/16th added to the top of the trigger to engage onto the bottom of the hammer.
Also looking for someone that can make me a spring for this Muff Pistol. Appreciate any leads you can offer. Willing to ship or drive from Belleville On.
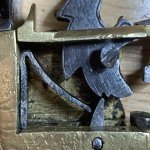