I have inherited this press with a trunk load of other reloading stuff from a friend. It works OKish, not perfect but not bad neither.
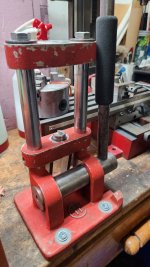
All dies I bought from a single brand LEE Wilson, no mixing.
I am developing my own processes now, brass preparation and seizing OD and ID. Chasing the steps for most consistency.
When I am neck seizing or pushing a mandrel into the brass neck, I feel a different force in between the brass shells.
Just pulling the handle down by hand and how hard is it is speculative, I would like to get something with numbers. Not that the torque numbers are important but to see visually a consistency.
I can pre-sort the neck tension before I got to a next step for bullet seating.
Tinkering to fabricate some kind of torque arm for it. Not as a torque wrench but the old style beam torque scale? Something like this maybe?
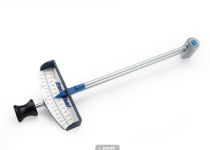
I would welcome some ideas.
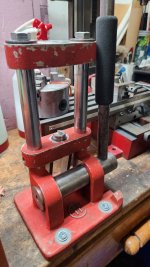
All dies I bought from a single brand LEE Wilson, no mixing.
I am developing my own processes now, brass preparation and seizing OD and ID. Chasing the steps for most consistency.
When I am neck seizing or pushing a mandrel into the brass neck, I feel a different force in between the brass shells.
Just pulling the handle down by hand and how hard is it is speculative, I would like to get something with numbers. Not that the torque numbers are important but to see visually a consistency.
I can pre-sort the neck tension before I got to a next step for bullet seating.
Tinkering to fabricate some kind of torque arm for it. Not as a torque wrench but the old style beam torque scale? Something like this maybe?
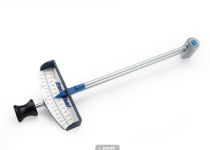
I would welcome some ideas.