I've been making some Minie balls from sheet lead and I've been getting this scum on top of the melt and it ends up in the nose of the Minie ball.
I've been fluxing like mad and it seems to generate even more scum.
I thought that my pieces of lead sheet were contaminated and I washed them as well.
Someone on the cast boolit board mentioned that he had to cast with the heat turned up high so I was casting at 10 on the Lee furnace.
I cleaned out the pot and tried again at level 8 and uncontaminated metal and the balls came out very nice.
I added a small brick with a small amount of scum and fluxed well and things went well.
I added another ingot with a little more crud on it and things started going down the toilet.
The pot was crudded up big time and fluxing and skimming brought up more scum than I had added to the clean metal.
So now I have another 6 or 7 more pounds of crappy metal.
Does anyone have any ideas for the cause and especially a cure?
I have about 25 pounds of this junk and I don't want to have to toss it.
TIA
I've been fluxing like mad and it seems to generate even more scum.
I thought that my pieces of lead sheet were contaminated and I washed them as well.
Someone on the cast boolit board mentioned that he had to cast with the heat turned up high so I was casting at 10 on the Lee furnace.
I cleaned out the pot and tried again at level 8 and uncontaminated metal and the balls came out very nice.
I added a small brick with a small amount of scum and fluxed well and things went well.
I added another ingot with a little more crud on it and things started going down the toilet.
The pot was crudded up big time and fluxing and skimming brought up more scum than I had added to the clean metal.
So now I have another 6 or 7 more pounds of crappy metal.
Does anyone have any ideas for the cause and especially a cure?
I have about 25 pounds of this junk and I don't want to have to toss it.
TIA
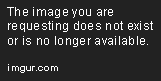