Might be that the person making it in BC was a former CGN member. I had picked up a bottle of it from a guy in BC, maybe 6 years ago. Great stuff. Very concentrated, a little bottle will last a lifetime if you only do a couple rifles a year.
Another good website/forum to check is www.finishing.com
That sounds like him. His used name was Lucky guy but I don't think he's a member any more.
I read on the LM instructions about making a scalding tank out of PVC pipe... which leads to my next question, when boiling the parts after rusting, is it necessary to keep it at a rolling boil for the duration, or will submerging it in scalding/boiled water for an equal ammount of time work as effectively? I do not mind building a metal tank to put on a burner at all if it will yield better bluing... im just curious.
As a positive note, the air outside my shop has been over 80% humidity for a long time... I think the gulf islands are made for this kind of teatment.
I can't speak to the scalding method. My technique is to bring the water to a rolling boil and keeping it there until I'm. done.
Even though the RH is 80%, at our recent temperatures of 0 to 5C, the air is holding too lttle moisture for effective rusting. Also, there is a risk of condensation on the metal that would really mess up the job.
Here's a couple of pictures of my set-up, etc
Damp Box. That's an old crock pot in the bottom to provide water vapour and heat. The upper bulb is on a rheostat and is used to control the RH. If the RH gets too high, I turn up the bulb to increase heat which in turn decreases RH.
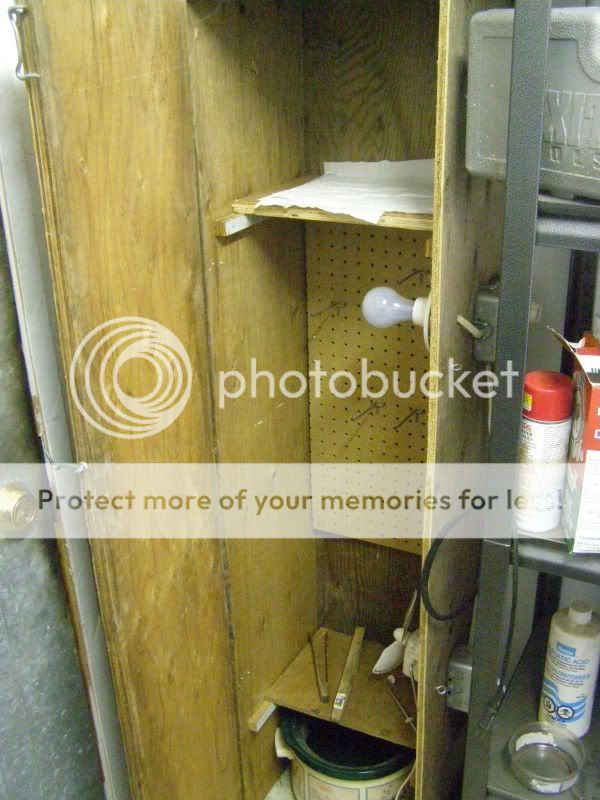
Drill press with a carding wheel that turns at about 500 rpm
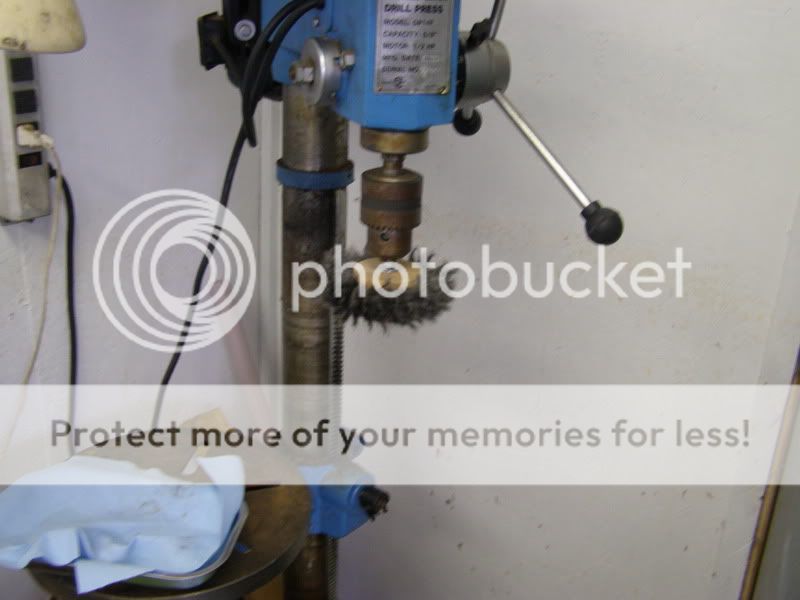
Boiling tray
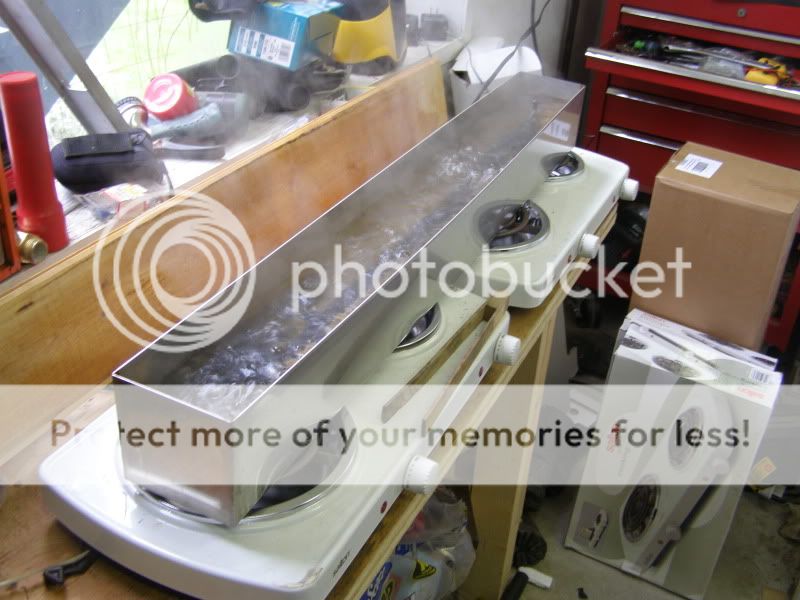
Rusted but not boiled

Boiled but not carded
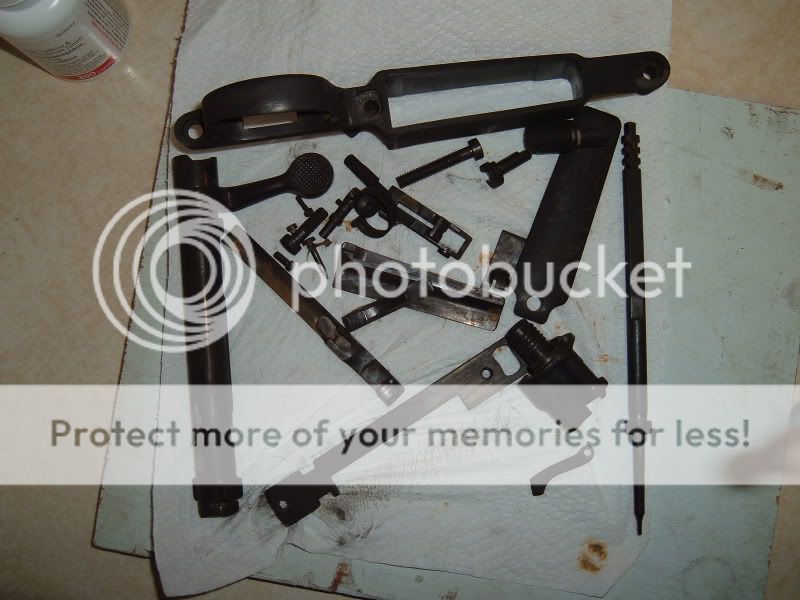
The finished product after 7 cycles
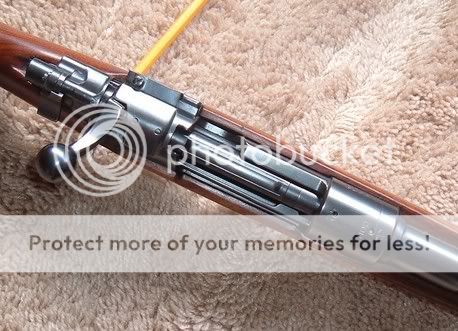
Last edited: