Hello everyone!
One day while cleaning up my garage I stopped to think for a bit after handling my armoured plate gongs....they were coated in very fine lead splatter from my centerfire rifles. After reflecting on how much I'd been shooting them (alot) and remembering the splatter patterns out on the range I started thinking about how much lead dust I was creating and bringing back home with me after every range session. Given the two little ones now running around and construction of a new private rifle range on some agricultural land the wife and I just aquired I committed to seriously investigate going lead free.
After being somewhat dissapointed at the slim pickings of what was at the time commercially available (not to mention the price!), I set out to see how hard it would be to have them made locally and wound up with my summer/fall project. Woohoo!
So I did up some basic drawings and shopped them out to some local screw-machine-equipped-volume-production-small-parts shops; I found an outfit willing to play ball and we went through several prototypes. First out of the hopper were two solid tip designs intended for use in my .308 M1A/M14s and my .224 Swiss Arms Classic Green. We went through several iterations primarily monkeying with the fouling band depth/gemetry and boattail geometry and now have something that seems to work reasonably well.
Material wise they're machined from solid copper that has been alloyed with some exotic trace metals to improve machinability. It was a b*tch to source material, and I was very surprised how expensive it is. If I get set up to make a zillion the only way it would have a hope of working out would be to commit to a complete mill run of material (aka - $25k worth per diameter of material run...yikes!!) so the project warrants careful study before taking a step like that
The .308 projectile weighs in at 155 grains with an S10 secant ogive and a slightly rebated boattail. Despite not being able to seat the bullet long enough to touch the lands of my M14S while still making magazine length, in all three of the M14 type rifles I've seriously tested with my new bullets they perform better than my standard 155gr Sierra HPBT match loads...woohoo! I've only shot them out to the limit of my rifle range (which is 500 yards), so I don't know how they perform at longer range.
The .224 projectile was designed with a 62gr target weight with an S7.3 slightly secant ogive and slightly rebated boat tail. I can't tell the difference in accuracy between them and my 69gr HPBT match standard fare load for my swiss rifles, but they shoot well and I'm happy enough with them to give them a longer term test.
Early in the project we made some up with standard boattails for comparison, however in my testing I could not get them to fly as accurately as the rebated boattails (don't know why) so I stuck with the rebated design.
I did a larger run (5000 bullets) for my own personal use as well as to try and understand the economics of mass production; the shop is still studying their learnings from the machine runtimes and program sequence (they're run on two separate axis so there is no partoff nipple like what you see on the backend of the barnes solids) to try and figure out what their bare bones price is; it's way premature to try and speculate as to whether or not they're commercially viable and would be made generally available. If the numbers come back and they look like they are in the ballpark, I'll go through the appropriate motions to get setup as a dealer and then get setup to sell them but in the meantime I'm good to go for a bit on my range while I do some longer term testing.
The solids are very gentle on my steel targets; moreso than any hollow point shot at similar velocity. I speculate that this is because there is no small pocket of air that gets compressed and then released at high temperature.
After getting the kinks worked out of the solids we did up some .308 hollow points just in time for hunting season. They were based on the solid profile but elongated in the rear driving band to accomodate material theived from the front end to make the hollowpoint. The cavity was initially drilled and then broached with a hex head, the idea being that hopefully the tip would shear along the corners of the hex head to behave like the barnes bullets do in tissue. For the tip we spun up some UHDPE to the profile of the original tip with a long stem for stabbing into the hollowpoint. My intent was to try and recover one from an animal shot this hunting season, however everything I dropped the hammer on (2 whitetail and 2 mule deer) wound up with complete penetration and no bullet recovery. There was no evidence of multiple exit wounds so I speculate the bullet is holding together well however I was dissapointed not to be able to report with a photograph of a recovered bullet amd admitantly my sample group is very small. Exit wounds and internal damage seem analagous to other animals I've seen shot with Barnes bullets. I've got some gelatin en-route to mix up early in the new year where I'll recover a bunch to see what's going on, both in the expansion world as well as a more observation based study of the fouling band performance and will report back as I go.
Regarding the tips - they were surprisingly a b*tch to machine (more of a material sorting problem...how to recover the tips from the chips but also some partoff issues with small ribbons remaining) and there is definately more work to do there before the hunting bullets would ever be commercial. They did work very well vis a vis functioning in my M14...I have a couple rounds that have been stripped by the bolt, rammed into the feed ramps, and then not fired to be used another time...the tips hold up well enough that there is no deformation or change in concentricity. All in all very happy with them other than reported difficulty in manufacturing. In our next batch we may try some delrin to see if it is any better. If money were no object I'd make them out of aluminum.
Anyway...I thought I'd make a post here about my fall project and see what you folks had for feedback! Critisism (preferably constructive) is encouraged....
Profile would be easy to change (ie: making a less aggressively tapered ogive designed for closer seating proximity to the throat/rifling while still making 2.800 for magazine length...I have my own thoughts on this but thought I'd throw it out there for other folks to weigh in on).
Enough of me blabbing....what do you think??
Thanks for looking/reading,
Brobee
One day while cleaning up my garage I stopped to think for a bit after handling my armoured plate gongs....they were coated in very fine lead splatter from my centerfire rifles. After reflecting on how much I'd been shooting them (alot) and remembering the splatter patterns out on the range I started thinking about how much lead dust I was creating and bringing back home with me after every range session. Given the two little ones now running around and construction of a new private rifle range on some agricultural land the wife and I just aquired I committed to seriously investigate going lead free.
After being somewhat dissapointed at the slim pickings of what was at the time commercially available (not to mention the price!), I set out to see how hard it would be to have them made locally and wound up with my summer/fall project. Woohoo!
So I did up some basic drawings and shopped them out to some local screw-machine-equipped-volume-production-small-parts shops; I found an outfit willing to play ball and we went through several prototypes. First out of the hopper were two solid tip designs intended for use in my .308 M1A/M14s and my .224 Swiss Arms Classic Green. We went through several iterations primarily monkeying with the fouling band depth/gemetry and boattail geometry and now have something that seems to work reasonably well.
Material wise they're machined from solid copper that has been alloyed with some exotic trace metals to improve machinability. It was a b*tch to source material, and I was very surprised how expensive it is. If I get set up to make a zillion the only way it would have a hope of working out would be to commit to a complete mill run of material (aka - $25k worth per diameter of material run...yikes!!) so the project warrants careful study before taking a step like that
The .308 projectile weighs in at 155 grains with an S10 secant ogive and a slightly rebated boattail. Despite not being able to seat the bullet long enough to touch the lands of my M14S while still making magazine length, in all three of the M14 type rifles I've seriously tested with my new bullets they perform better than my standard 155gr Sierra HPBT match loads...woohoo! I've only shot them out to the limit of my rifle range (which is 500 yards), so I don't know how they perform at longer range.
The .224 projectile was designed with a 62gr target weight with an S7.3 slightly secant ogive and slightly rebated boat tail. I can't tell the difference in accuracy between them and my 69gr HPBT match standard fare load for my swiss rifles, but they shoot well and I'm happy enough with them to give them a longer term test.
Early in the project we made some up with standard boattails for comparison, however in my testing I could not get them to fly as accurately as the rebated boattails (don't know why) so I stuck with the rebated design.
I did a larger run (5000 bullets) for my own personal use as well as to try and understand the economics of mass production; the shop is still studying their learnings from the machine runtimes and program sequence (they're run on two separate axis so there is no partoff nipple like what you see on the backend of the barnes solids) to try and figure out what their bare bones price is; it's way premature to try and speculate as to whether or not they're commercially viable and would be made generally available. If the numbers come back and they look like they are in the ballpark, I'll go through the appropriate motions to get setup as a dealer and then get setup to sell them but in the meantime I'm good to go for a bit on my range while I do some longer term testing.
The solids are very gentle on my steel targets; moreso than any hollow point shot at similar velocity. I speculate that this is because there is no small pocket of air that gets compressed and then released at high temperature.
After getting the kinks worked out of the solids we did up some .308 hollow points just in time for hunting season. They were based on the solid profile but elongated in the rear driving band to accomodate material theived from the front end to make the hollowpoint. The cavity was initially drilled and then broached with a hex head, the idea being that hopefully the tip would shear along the corners of the hex head to behave like the barnes bullets do in tissue. For the tip we spun up some UHDPE to the profile of the original tip with a long stem for stabbing into the hollowpoint. My intent was to try and recover one from an animal shot this hunting season, however everything I dropped the hammer on (2 whitetail and 2 mule deer) wound up with complete penetration and no bullet recovery. There was no evidence of multiple exit wounds so I speculate the bullet is holding together well however I was dissapointed not to be able to report with a photograph of a recovered bullet amd admitantly my sample group is very small. Exit wounds and internal damage seem analagous to other animals I've seen shot with Barnes bullets. I've got some gelatin en-route to mix up early in the new year where I'll recover a bunch to see what's going on, both in the expansion world as well as a more observation based study of the fouling band performance and will report back as I go.
Regarding the tips - they were surprisingly a b*tch to machine (more of a material sorting problem...how to recover the tips from the chips but also some partoff issues with small ribbons remaining) and there is definately more work to do there before the hunting bullets would ever be commercial. They did work very well vis a vis functioning in my M14...I have a couple rounds that have been stripped by the bolt, rammed into the feed ramps, and then not fired to be used another time...the tips hold up well enough that there is no deformation or change in concentricity. All in all very happy with them other than reported difficulty in manufacturing. In our next batch we may try some delrin to see if it is any better. If money were no object I'd make them out of aluminum.
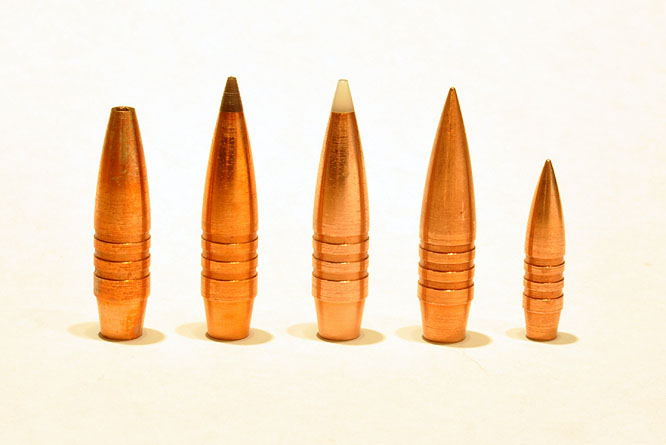
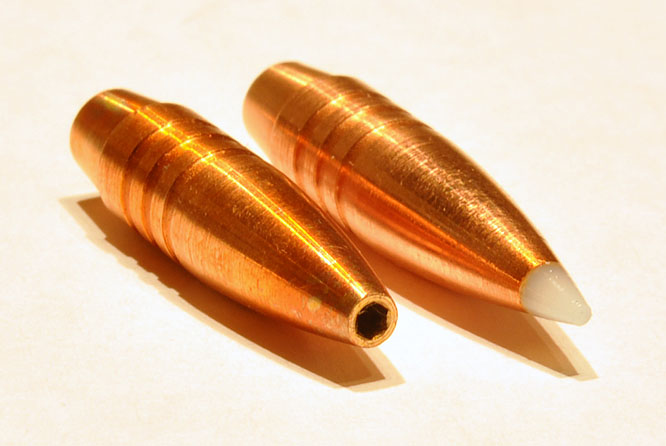
Anyway...I thought I'd make a post here about my fall project and see what you folks had for feedback! Critisism (preferably constructive) is encouraged....
Enough of me blabbing....what do you think??
Thanks for looking/reading,
Brobee