More importantly...how does the back side of the slide look?
Was it purged during the process?
Penetration %?
A surface bead is NOT structural integrity.
There were only three pictures shown on that particular job. There was no discussion of purging, penetration, etc, it was generally about the process being beyond normal welding.
Other jobs, for example, were on cracked top straps on revolvers which were put back into use. Put back into use presumes there was structural integrity - particularly in the US with it's high ratio per capita of slip and fall lawyers running around looking for clients for their next lawsuit.
I doubt many gunsmiths in the US (and whoever provides them with their acts and omissions insurance coverage) would say "good to go" and give their customer back a rifle or handgun that had the potential to blow up when fired after the welding job.
I am not a gunsmith nor am I a welder, my father was a welder/millwright and my grandfather a machinist; that and occasionally hanging out in the shops of local gunsmiths like Bill Leeper and Martin Hagn doesn't qualify me for anything other than being interested in gunsmithing operations.
But as perhaps an interesting trivia point, I did spend most of last year as the operations manager trying to get the failed carcass of what was once Montana Rifle Company up and running again. Among the records I found were one where 84 cracked receivers for their Professional Hunter series rifles were sent off to have the cracks welded. Records showed the actions were destined to be used to build .505 Gibbs, 416 Rigby, 460 Weatherby, etc. rifles.
The records show the returned actions went straight into the final fitting and finishing stage on the upper floor.
In contrast, in another case of fixing defects, badly warped castings due to core slump were not rejected and returned to the company doing the casting. Instead, shop workers were given hydraulic presses and jigs made by PTG to straighten them out as best they could. The straightened castings were then sent to a business back east for heat treating and annealing before returning to MRC where those castings were then put into the CNC fixtures in the Haas machines and turned into a MRC action. (And many of them were hell for the shop as when those receivers were blued after heat treating and annealing, the bluing had a mottled appearance).
I remember that well because I was mildly curious about heat treating and annealing before doing the CNC operations to turn them into receivers; I would have thought they'd heat treat and anneal after the machining operations were completed. I think I might have scanned and emailed Bill Leeper some of that paperwork for his amusement...
The difference (to me), is there was no paper trail evidence of any heat treating/annealing of the cracked receivers after welding, as there was for the banana shaped castings that were bent back into a shape that would fit into the fixtures in the CNC machines for machining into actions. Suggests that the welding was pretty good as done, perhaps.
That's about all I can contribute to the discussion... other than to circle back to the initial post with a bolt reshape job Bill did on a couple of my Huskys because I found the blued Mannlicher look much more pleasing to the eye than the stock silvery round ball bolt the rifle came with. How Bill converted the original stem and ball bolt to the Mannlicher style, I can't recall:
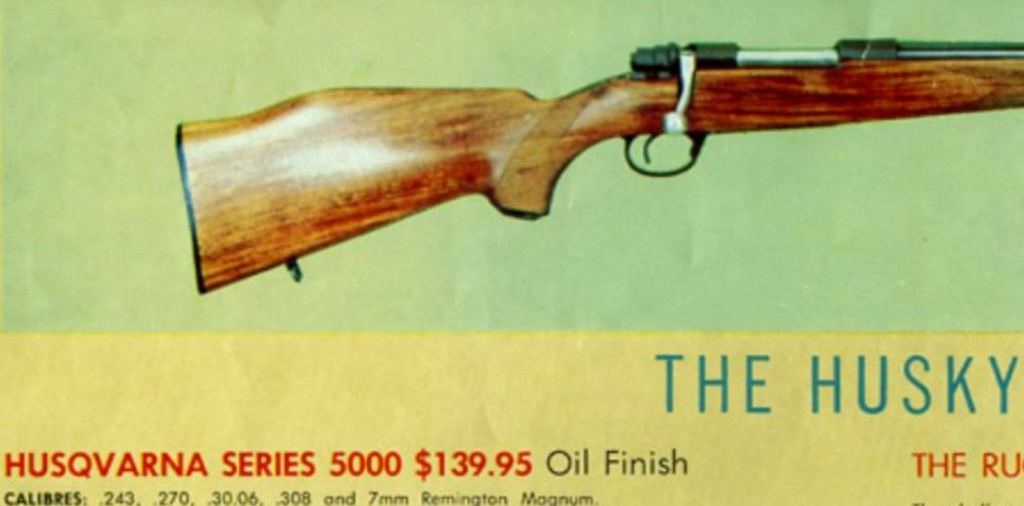
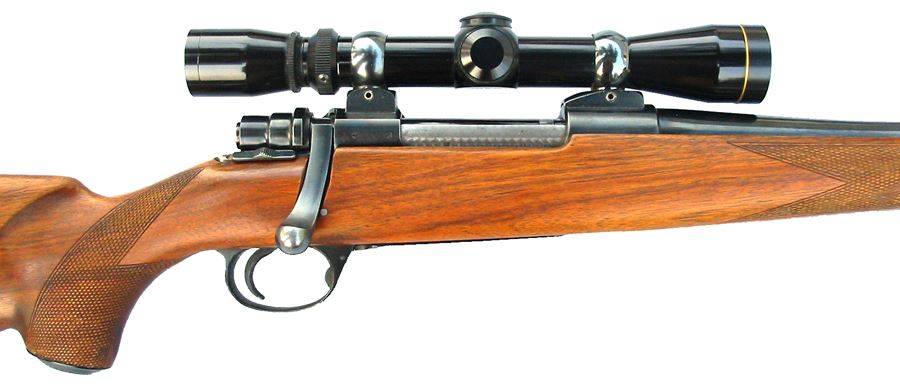