After sitting on the needed equipment for several months, had a chance to make my first attempt at casting some Minies for my Parker Hale Musketoon. The mold is an old OHaus 58-500 , which apparently is now sold by RCBS. Bottom plug is from the P-H 58560 mold which gives a flat bottomed Minie. Lee melting pot had to be set on 10 to keep the lead molten long enough to pour the 560 grain Minies. Took a long time to get it hot enough to get some good castings- of the 21 that I ended with, probably 10 I would call good, 4 are OK and the rest have some flaws and will be re-melted and recast. Ones that had base skirt flaws went back in the bot right away. I was using some leftover lead balls but need to find some more pure lead. It's a start- the wooden bat and ladles came from local thrift shop. Next time I will try the Parker Hale mold as it has a bigger block and longer handles so I can get more heat into it and get better casts. Any tips or hints are welcomed from anybody with more experience at this! Fun Fun!
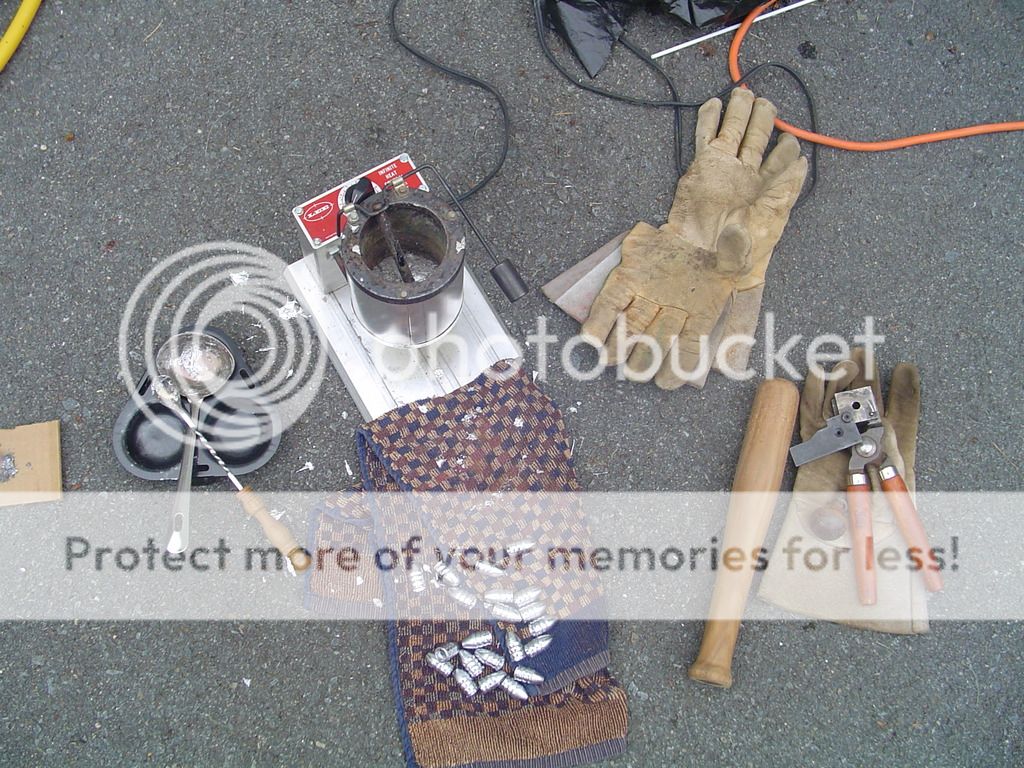
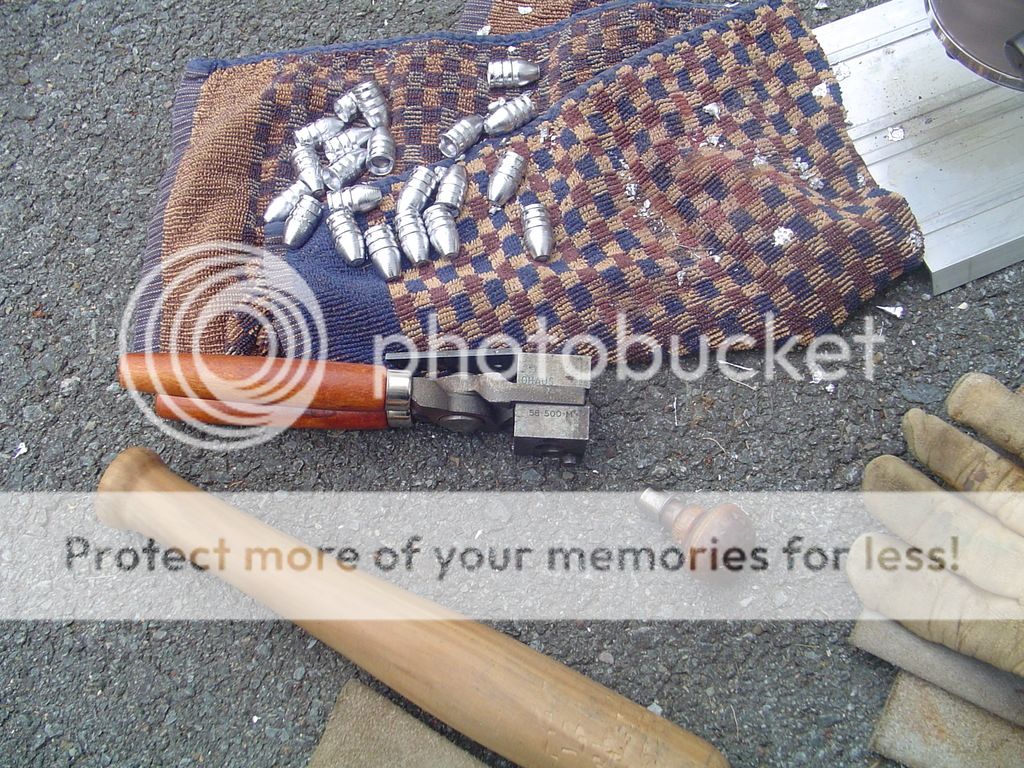
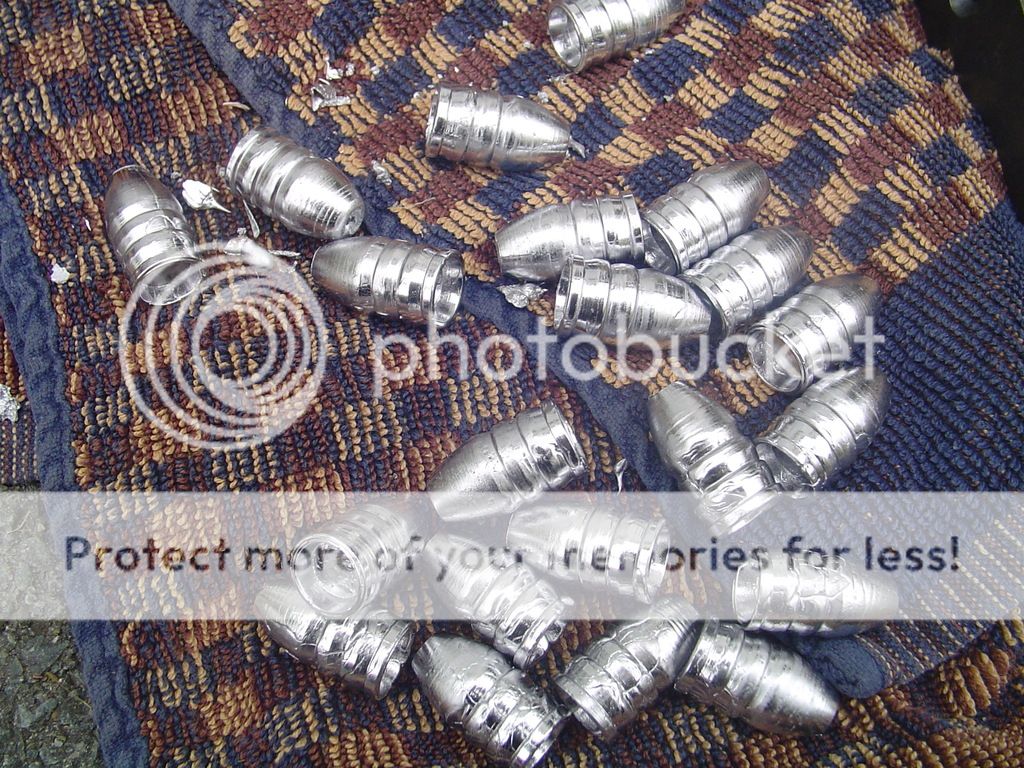
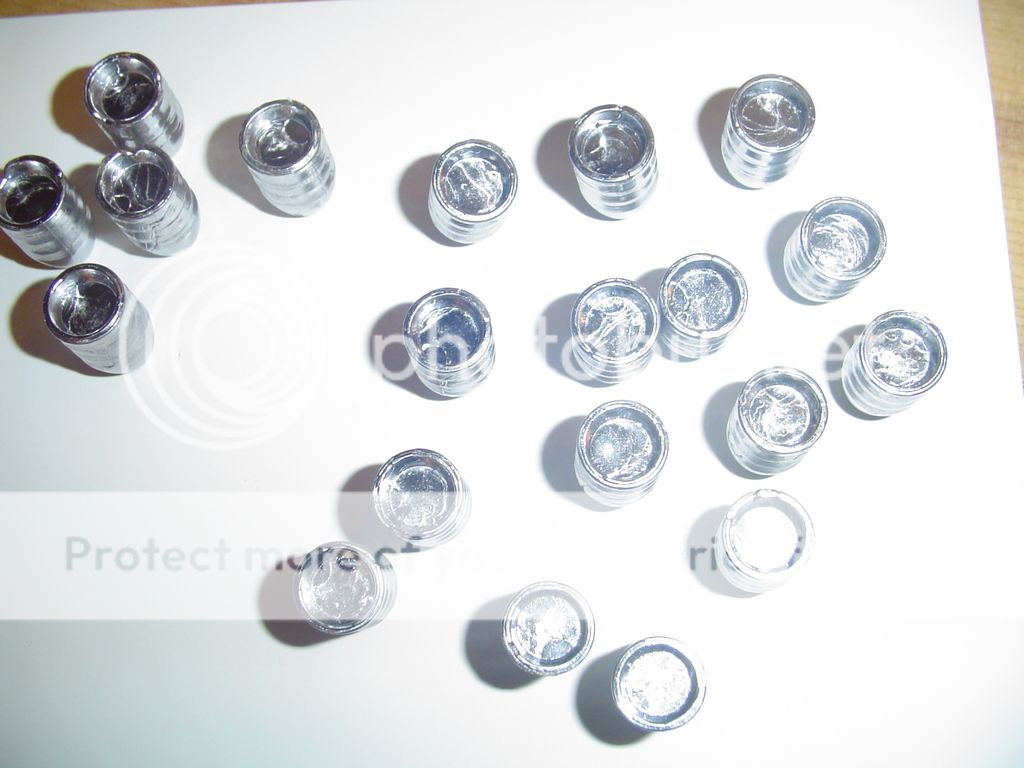
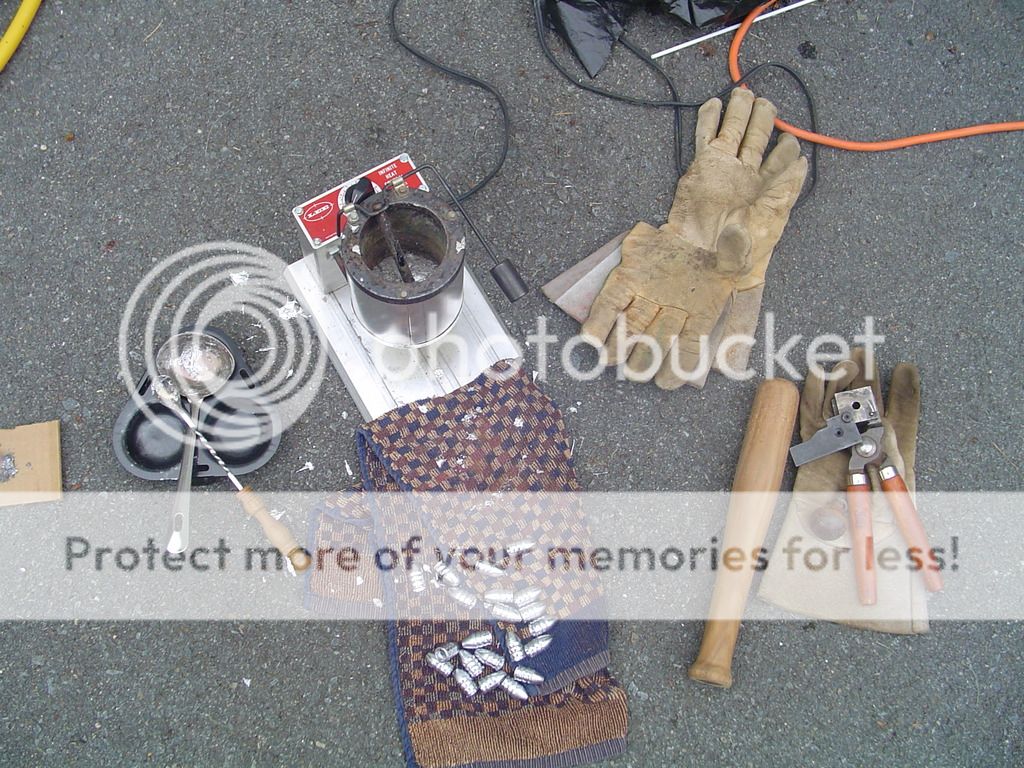
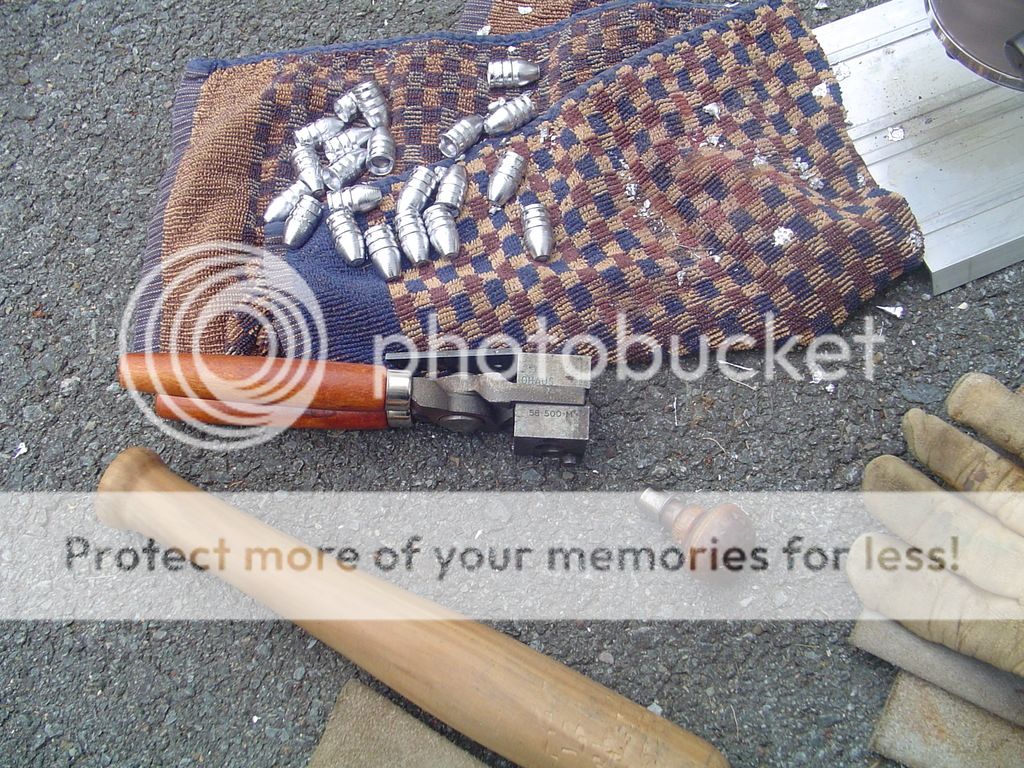
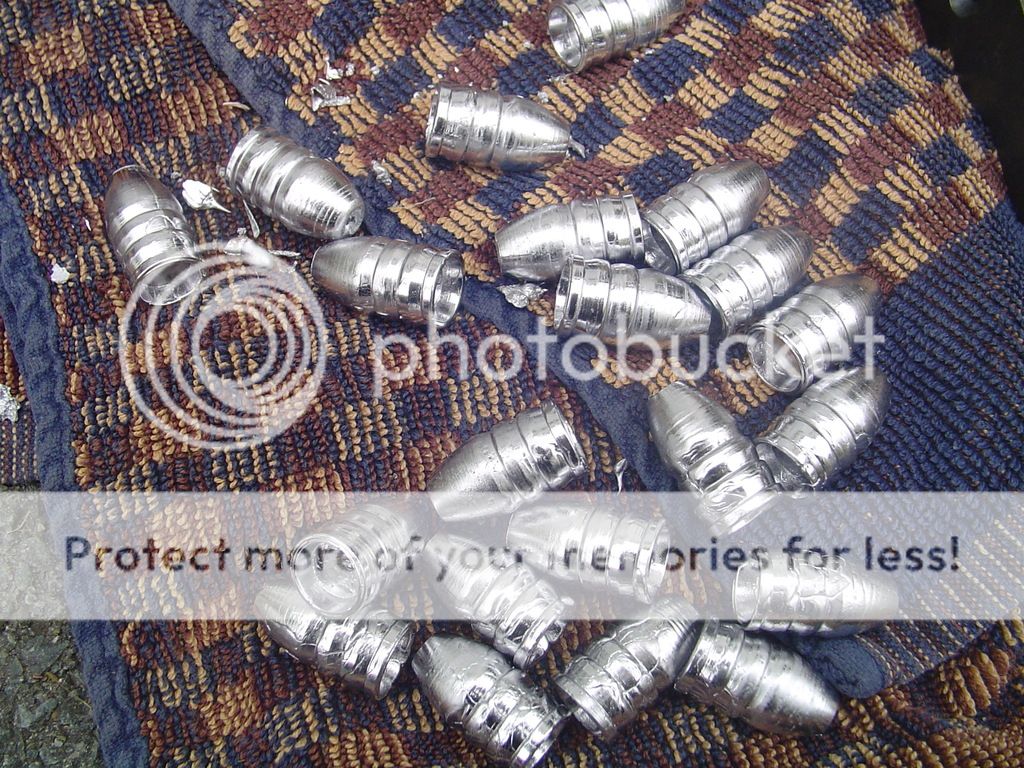
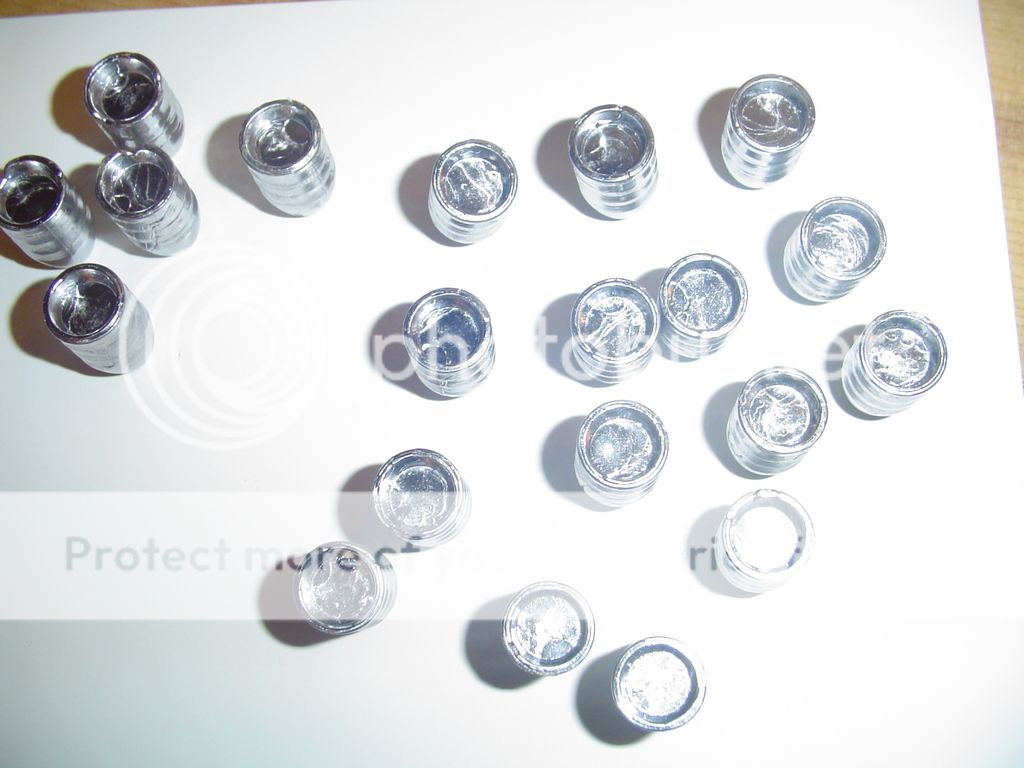