Leuchtkafer
Member
I've been wanting to get into PRS shooting, especially since my range started building out targets and barricades this year. As good excuse as any to build a rifle
I ordered up an MDT ACC Premier Gen 2 as soon as it became available for the 457 action and now have it in my possession. I got my butt into gear this week to start fitting the barrel. I like the setup with a 4-jaw chuck and a spindle spider (which I made) to do barrel work. This is a 0.900" Shilen barrel. Finished length from shoulder to muzzle came out at 17.5" and total length including tenon is 18-11/16".
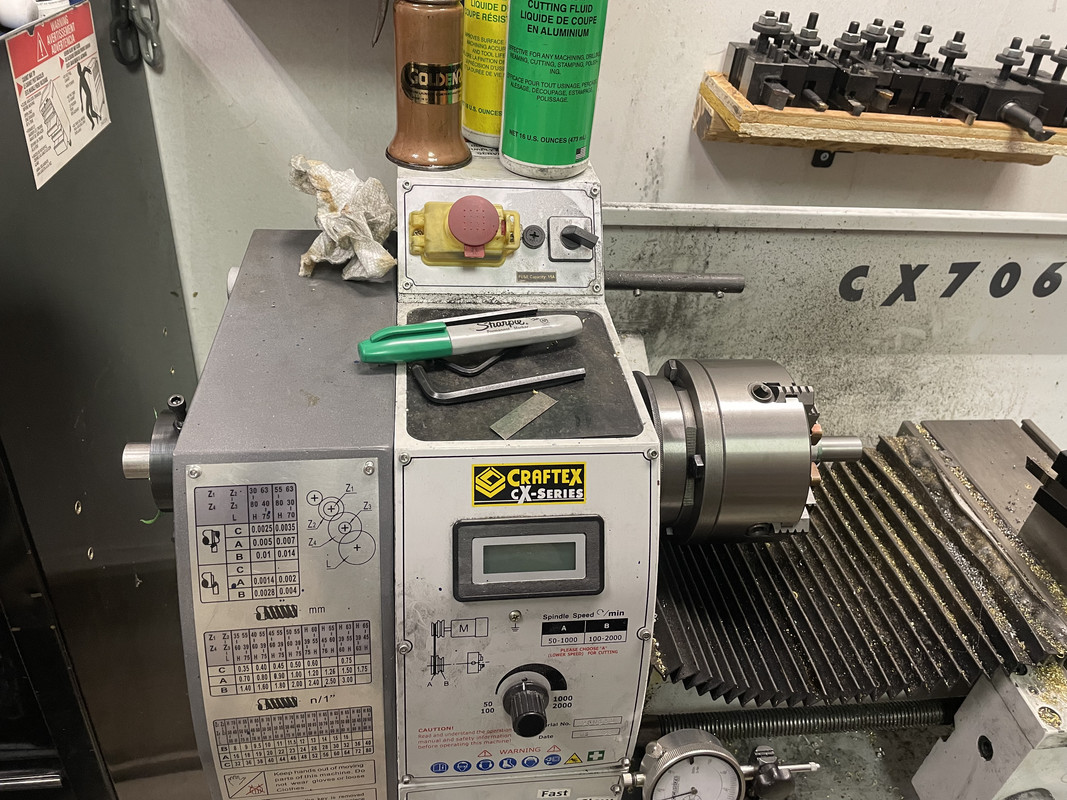
Got the tenon cut and it's time to chamber. The pilot size on this barrel is 0.2166"
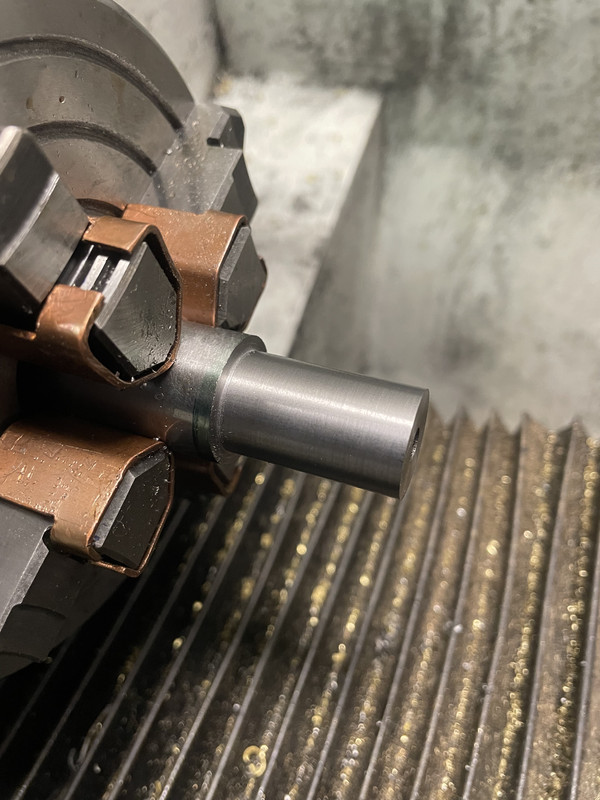
I was curious by how much the bore is out from the outer diameter of the barrel, so I measured it before dialing in the bore for chambering. This bore is running out about 0.003". All things considered with what's involved in deep drilling a blank, that ain't bad, I was expecting more.

I upgraded the DRO on my tailstock since I did the factory barrel experiment, the previous unit would power off after a time and lose it's zero, very annoying. This unit remembers it's last zero if it powers off, much better. The stainless machines easier than the factory barrel carbon steel, I can really tell the difference while reaming by hand. It's kinda like fishing, but in reverse. Little "nibbles" are OK, back off a bit if you feel a big nibble, but the last thing you want is a big bite!
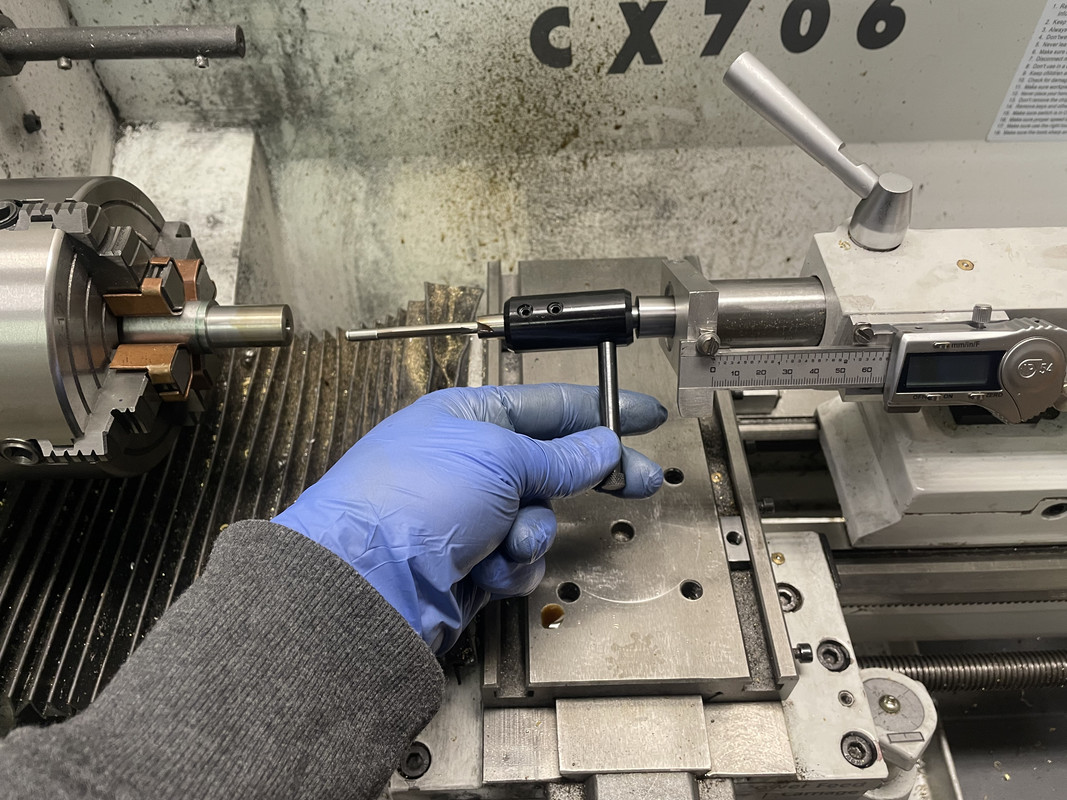
The copper chuck jaw caps and brass tipped screws in the spider do a great job of protecting the barrel finish, there's not a mark on it from them.
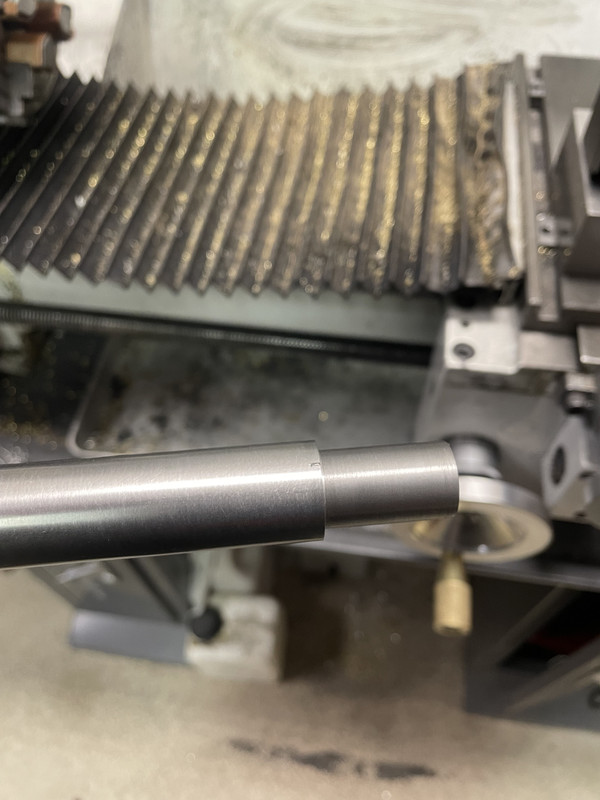
I'll update as I move this build along, before I changeover to a milling setup to cut the extractor slots, I've got another barrel to fit to an action and chamber so just to streamline my workflow I'm going to do all the work on both barrels in one setup before I do a major tooling change. I also have to crown them before the milling changeover, that just involves swapping out my solid tool post mount for the compound slide, but I'll chamber the second barrel first since I only want to setup the compound angle for the crown once and then do both barrels.
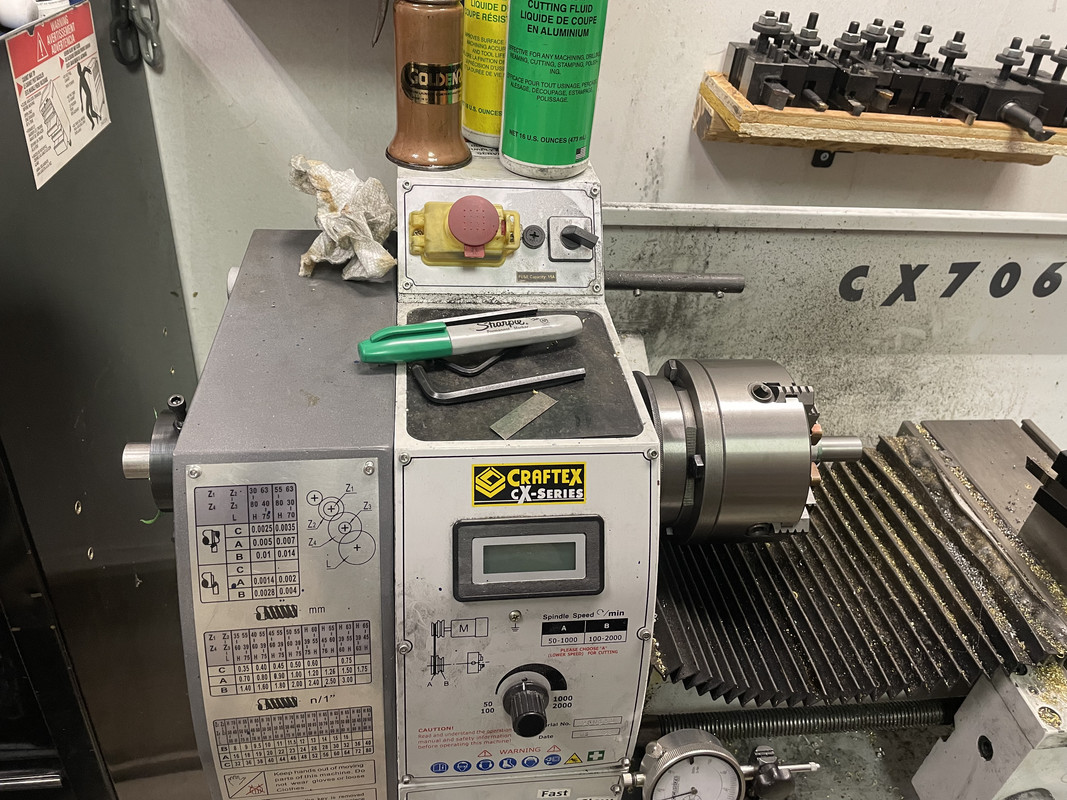
Got the tenon cut and it's time to chamber. The pilot size on this barrel is 0.2166"
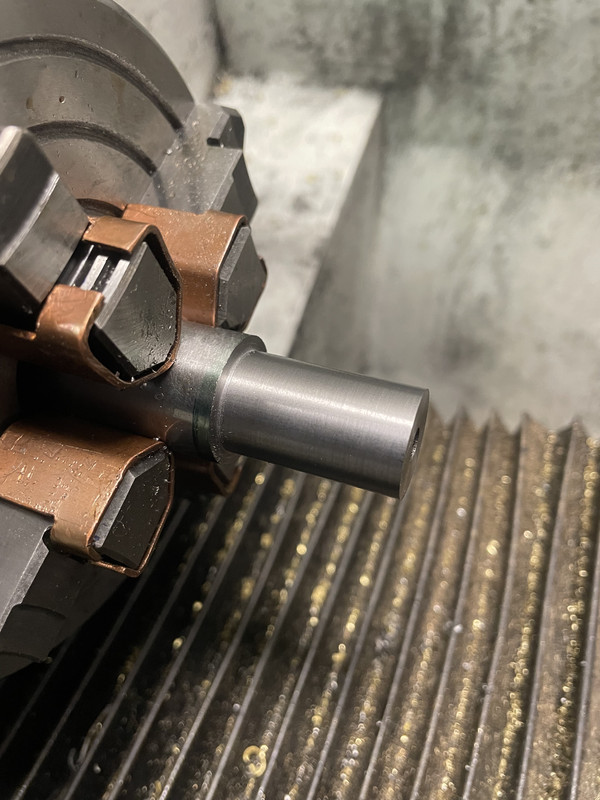
I was curious by how much the bore is out from the outer diameter of the barrel, so I measured it before dialing in the bore for chambering. This bore is running out about 0.003". All things considered with what's involved in deep drilling a blank, that ain't bad, I was expecting more.

I upgraded the DRO on my tailstock since I did the factory barrel experiment, the previous unit would power off after a time and lose it's zero, very annoying. This unit remembers it's last zero if it powers off, much better. The stainless machines easier than the factory barrel carbon steel, I can really tell the difference while reaming by hand. It's kinda like fishing, but in reverse. Little "nibbles" are OK, back off a bit if you feel a big nibble, but the last thing you want is a big bite!
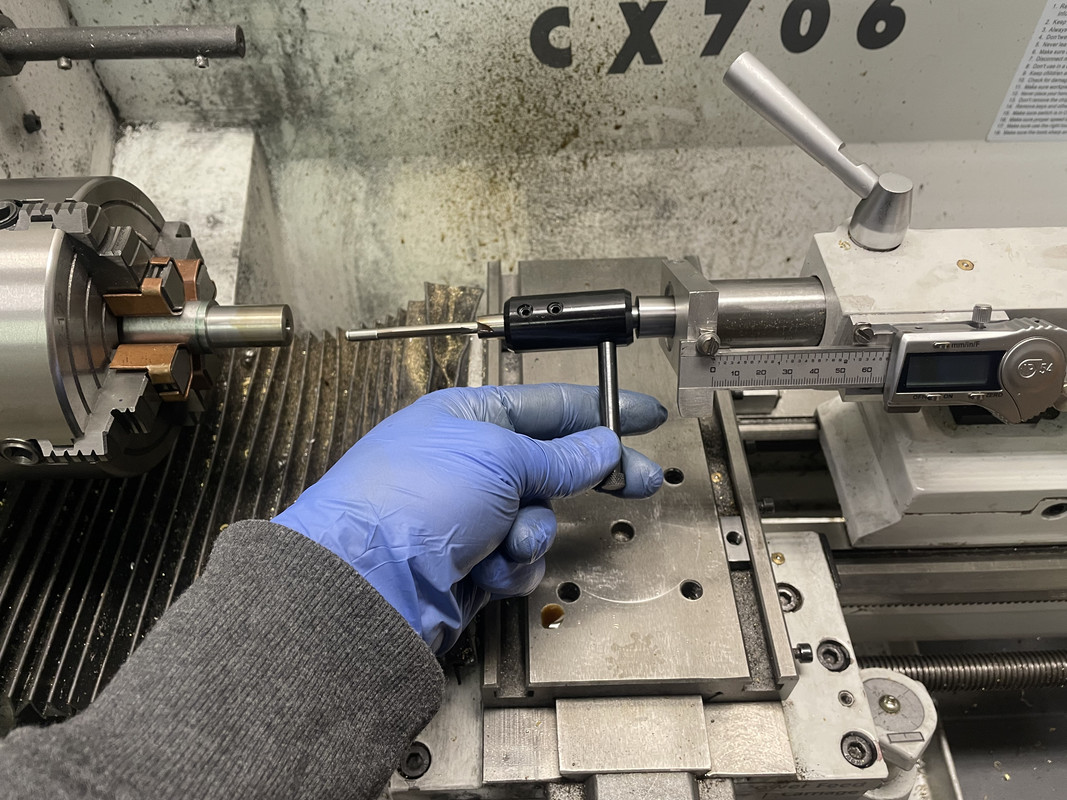
The copper chuck jaw caps and brass tipped screws in the spider do a great job of protecting the barrel finish, there's not a mark on it from them.
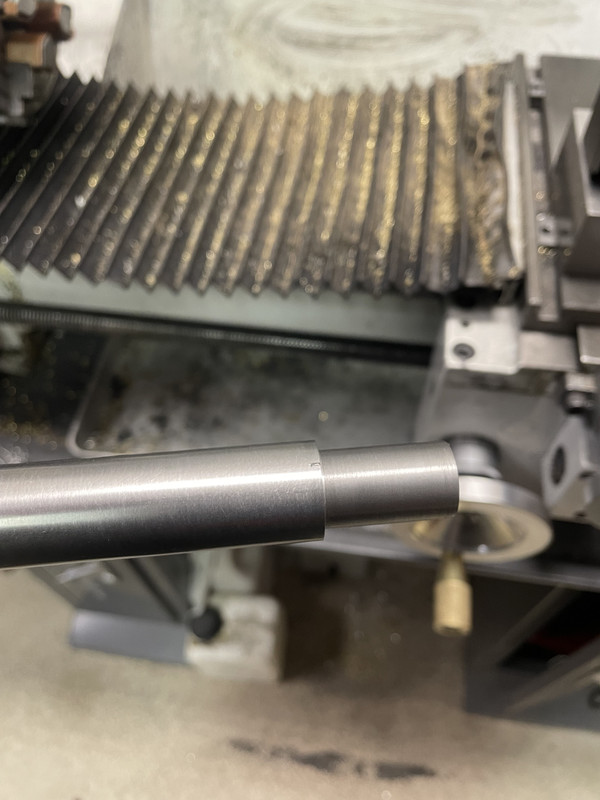
I'll update as I move this build along, before I changeover to a milling setup to cut the extractor slots, I've got another barrel to fit to an action and chamber so just to streamline my workflow I'm going to do all the work on both barrels in one setup before I do a major tooling change. I also have to crown them before the milling changeover, that just involves swapping out my solid tool post mount for the compound slide, but I'll chamber the second barrel first since I only want to setup the compound angle for the crown once and then do both barrels.
Last edited: